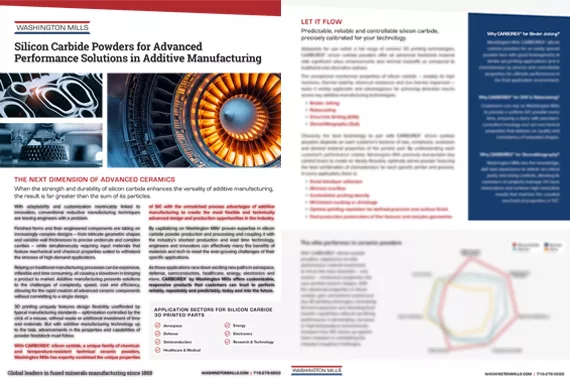
Next-Gen Performance Solutions in 3D Printing
Breathe life into your most advanced designs with the strength and stability of silicon carbide.
Additive manufacturing, a technology that’s been around for nearly 30 years, has become increasingly more widespread offering possibilities for future product development. It is the process of creating a structure made by the addition of thousands of tiny layers, when combined, create a product. Computer and CAD software assists when designing and “printing” the desired shape.
Breathe life into your most advanced designs with the strength and stability of silicon carbide.
3D ceramic printing affords manufacturers the ability to produce ceramic structures with more complex geometries or on smaller scale than can be obtained from traditional investment casting or machining techniques. Printing of ceramic parts is typically accomplished by mixing ceramic particles in a liquid binder system (slurry based). The binder can be activated by photopolymerization, but direct extrusion and inkjet printing are also possible. Following printing, ceramic parts typically require post processing (green body sintering) to obtain a densified ceramic structure. Direct powder sintering techniques are also possible, though not widely used. Washington Mills’ fine ceramic powders, including white aluminum, silicon carbide and boron carbide, are produced to highest quality standards to deliver consistent process results. Powder distributions can be tailored so customers can modify their slurry to suit their printing requirements.
A distinctive benefit of additive manufacturing is the greater range of shapes and designs that can be manufactured in one piece creating a stronger product that doesn’t have weak areas that can be compromised.
Washington Mills manufactures silicon carbide and aluminum oxide powders that are used in additive manufacturing applications such as gas turbine engines, aluminum (AMC) and ceramic matrix composites (CMC). The chemical and physical properties of silicon carbide make it an excellent material for high temperature structural applications, such as gas turbine engine components. Properties include excellent oxidation resistance and corrosion resistance, high thermal conductivity, low thermal expansion coefficient, high resistance to thermal shock and high strength at elevated temperatures. Washington Mills Ceramics Corporation produces specially formulated 3DCM and 3DPM for mass finishing of 3D printed parts.
Finish your printed part with Washington Mills Ceramics and our Parts Processing Lab
Washington Mills offers the ability to select a product based on the industry served or how the material works.